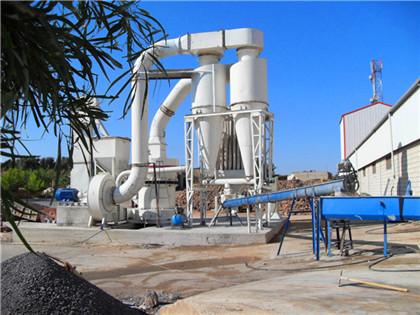
1、技術來源
連續酸解技術最早從韓國引進,重慶化工設計研究院有限公司在消化吸收原韓國引進技術的基礎上,對連續酸解裝置進行了全面的技術提升,從設備結構、材質到工藝參數都進行了優化改進,由此形成自己的專有技術。
2、基本原理
鈦精礦(主要為FeTiO3)在一定溫度下,與硫酸反應生成硫酸氧鈦,硫酸氧鈦易溶于水,而形成酸解液,酸解液經進一步處理得鈦白粉。連續酸解是硫酸法鈦白粉的一個關鍵工段,對其生產起著至關重要的作用。
主要反應方程式如下:
FeTiO3+3H2SO4==Ti(SO4)2 + FeSO4+ 3H2O
FeTiO3+2H2SO4==TiOSO4+ FeSO4 + 2H2O
Fe2O3+3H2SO4==Fe2(SO4)3+ 3H2O
3、工藝過程
工藝過程包括預混、酸解、浸取、還原、尾氣洗滌五個工序。
(1)預混
將98%濃硫酸與磨好的鈦精礦粉預先充分混合潤濕。
(2)酸解
將預混料與稀酸按比例加入反應器中進行反應。
(3)浸取
酸解反應器出來的物料直接進入溶解槽進行浸取,得酸解液。
(4)還原
用鐵粉將酸解液中的三價鐵還原為亞鐵離子,以便后工序除鐵。
(5)尾氣洗滌
酸解尾氣經急冷除塵除酸霧后,堿洗除二氧化硫,最后高空排放。
4、技術特點
(1)實現了全過程的DCS控制,減少了操作人員。
(2)單套產能達2.0~2.5萬噸/年。
(3)反應器攪拌軸使用壽命達一年以上。
(4)酸解率高,產品質量穩定。
(5)酸解尾氣穩定達標排放,環境效益顯著。
(6)消除了酸解“冒鍋”等安全隱患,實現了本質安全。
5、技術水平
本連續酸解技術目前處于世界先進水平,超越國內外其他酸解技術。
6、能源消耗
能源消耗見下表1所示。
表1 連續酸解消耗量(以1噸鈦白粉計)
公用工程名稱 |
額定消耗量 |
備 注 |
酸解主裝置(電) |
150kWh |
|
尾氣處理(電) |
2.5kWh |
|
蒸汽(0.7MPa) |
85kg |
|
7、節能減排狀況
連續酸解工藝完全解決了間歇酸解尾氣瞬時排放量太大的問題,使酸解尾氣像煅燒尾氣一樣均勻穩定地排放,從而使酸解尾氣易于處理,并實現穩定達標排放。
8、技術應用條件
凡是采用硫酸法生產鈦白粉的廠均可進行改造,變間歇酸解為連續酸解。
9、應用實例
實例1:廣東云浮市惠沄鈦白股份有限公司3萬噸/年硫酸法金紅石鈦白粉工程
實例2:攀鋼集團重慶鈦業有限公司75kt/年硫酸法鈦白技術改造升級搬遷項目連續酸解工程
實例3:印度KILBURN CHEMICALS LIMITED,INDIA 15,000噸/年銳鈦型鈦白粉項目
實例4:印度SARAF AGENCIES (P) LTD.,INDIA 30,000噸/年金紅石型鈦白粉項目
10、經濟效益
經濟效益測算見下表2所示。
表2 連續酸解與間歇酸解運行費用估算(以1噸鈦白計)
名稱 |
單價 |
間歇酸解 |
連續酸解 |
連續酸解比間歇酸解節約的費用 |
數量 |
價格(元) |
數量 |
價格(元) |
元/噸 |
酸解主裝置(電) |
0. 7元/kWh |
83kWh |
58.1 |
150kWh |
105 |
-46.9 |
尾氣處理費用(電) |
0. 7元/kWh |
12.8Wh |
9.0 |
2.5kWh |
1.75 |
7.25 |
鈦精礦 |
1250元/噸 |
2.355t |
2944 |
2.282t |
2852.5 |
91.5 |
98%硫酸 |
600元/噸 |
3.769t |
2261.4 |
2.684t |
1610.4 |
651 |
60%硫酸 |
300元/噸 |
0 |
0 |
1.750t |
525 |
-525 |
蒸汽費用 |
175元/噸 |
50kg |
8.75 |
85kg |
14.875 |
-6.125 |
少產廢硫酸(20%) |
-80元/噸 |
0 |
0 |
-5.32 t |
-425.32 |
425.32 |
主要設備維護費用 |
|
0 |
0 |
|
10 |
-10 |
按2萬噸/年產能計,每年節省費用約1254萬元,一年可收回投資 |
注:1、間歇酸解酸礦比為1.65,酸解率為94%;連續酸解酸礦比為1.60,酸解率為97%;
2、間歇酸解操作人員20人,連續酸解操作人員12人,按照每人每年10萬元計。
3、一臺反應器,一年槳葉損壞一次,維護費約為20萬元,折算至每噸鈦白約為10元。
與間歇酸解比較,連續酸解經濟效益明顯,節約的成本費用可一年收回投資。
(來源:中國石油和化工勘察設計協會) |