1、技術的來源
本技術來源于吉林省石油化工設計研究院。山梨醇和甘露醇、木糖醇、麥芽糖醇等都是可食用糖醇,同時又是生產維生素C、斯潘、吐溫及植物化工醇的原料,用途極為廣泛。目前,山梨醇已廣泛應用于醫藥、表面活性劑、日用化工、食品加工等行業,專有技術在于總結了傳統工藝(間歇,單釜)氫化反應的基礎上,開創了連續氫化新工藝,目的在于極大的提高生產效率和產品質量。
2、開發和研制
山梨醇的工業化生產主要是以葡萄糖加氫為主:在有催化劑存在一定溫度的條件下,氫氣在反應釜中與葡萄糖液發生還原反應,生成山梨醇。反應過程需要氫氣過飽和,為使得葡萄糖轉化率提高,氫化徹底,氫氣往往要過量,回收工藝復雜,差壓式固定床和漿料床反應器分步氫化就能很好的解決這一難題,為此連續氫化便產生,被定義為連續加氫新工藝。
3、加氫反應
葡萄糖加氫過程,會釋放出熱量,釜內氣體膨脹會造成系統超壓,帶來很大的危險性,通常采用安全閥來保護系統,系統超壓安全閥起跳,高溫高壓氣體釋放,帶走熱量的同時,釜內壓力降低。釋放的氣體即為氫氣和水蒸汽,雖然通過阻火器、高空排放等方式降低危險性,但依然是危險源,同時造成氫氣損失。兩步連續加氫技術的出現,一級釋放氫用于二級氫化反應,即降低了氫氣成本又提高了氫氣利用率。實現氫的利用率達到98%,糖液的氫化率達到99.8%以上,二級連續氫化率100%。
4、新技術操作過程:
(1)溶糖調配:將葡萄糖液調配至40~50%濃度,PH值調節至6~7,溫度50~90℃;
(2)氫化反應:調配好的葡萄糖溶液用泵連續不斷的泵入裝有催化劑的固定床反應器中,從反應器底部持續通入高壓氫氣,保持釜內壓力10.5~12.5MPa,溫度控制在90~130℃,物料停留時間短,空速比控制,出料得粗山梨醇;
(3)粗醇溶液出料又進入漿料床反應器,繼續氫化,反應結束后,經高壓冷卻器采用循環水降溫后,進入高壓分離器汽液分離,分離出的氫氣經過冷卻、再分離后返回壓縮機前(或變壓吸附前)被再次壓縮利用;
(4)沉降分離:分離完氫氣的粗醇液壓入低壓分離罐進行二次沉降分離,上清液進入脫色工序,分離下來的催化劑進行活化再生返回注料系統;
(5)粗醇精制:經沉降分離后的山梨醇溶液濃度約為45~50%,經脫色、過濾、離交、蒸發等步驟,獲得山梨醇成品;
(6)第(2)項中所述通入反應釜的高壓氫氣,為新制備的氫氣和回收的氫氣,新氫和回收氫比例為1:1~1:1.3;
(7)第(3)項中粗醇溶液初步冷卻后,在高壓分離器內分離出氫氣,氫氣被冷卻、再分離后返回壓縮機前再次壓縮利用或去變壓吸附前,重新凈化再壓縮。
5、新技術具有以下優點:
(1)本專有技術采用自動防飛溫超壓聯鎖控制系統,通過壓力聯鎖,釜底進氣,釜頂排氣,反應徹底,副反應少,產品殘糖低;
(2)本專有技術在反應釜排氣和高壓分離時,對氫氣進行回收、處理,使得氫氣能夠循環利用,設有排空或解釋排放,安全問題得到保證,節省投資,氫氣利用率高;
(3)兩段連續加氫,催化劑釜內截留使其單位消耗更低,凈化精制更容易,效果更好。
(4)裝置高壓反應器容積大,反應壓力高,氫化產品徹底,是Vc級醇生產的必由之路。
6、工藝流程
(1)流程示意圖(見附圖)
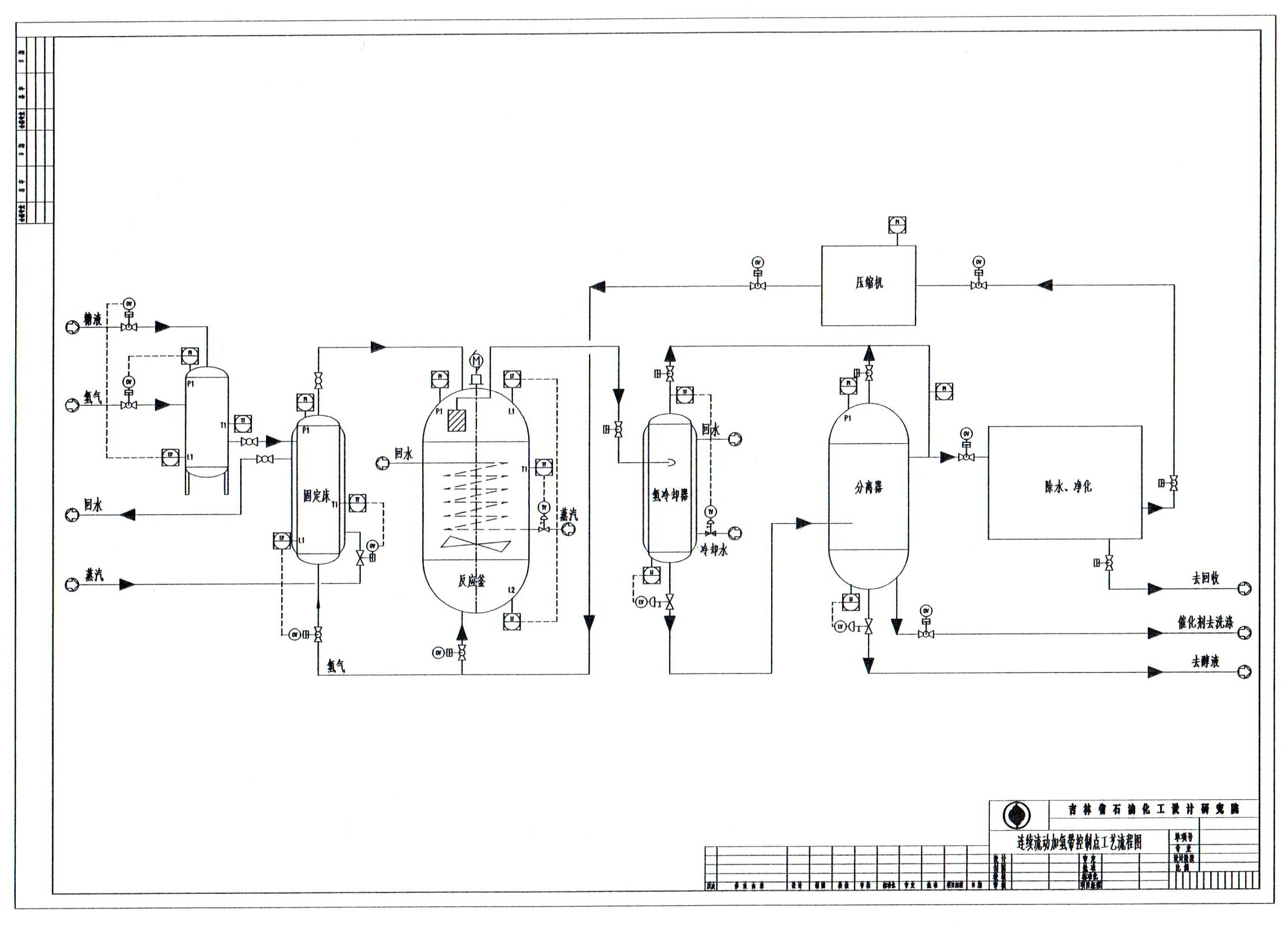
(2)連續加氫與傳統工藝的區別
a固定床和漿料床兩段連續加氫反應;
b固定床預氫化,還原程度達到90%,其余10%由漿料床繼續氫化完成;
c循環氫冷卻分離后再壓縮后進入氫氣系統再利用,無損耗和排放;
d釋放氫的壓力盡量保持不變,以減少動力的消耗;
e壓力范圍10.5-12.5MPa,溫度90-130℃,PH值在6-7,范圍變化小。
f氫化液清澈透明,精制凈化成本低,節省了過濾和脫色工序。
(3)連續加氫與國內外先進水平的比較
序號 |
項目 |
國外先進水平 |
本專有技術 |
國內現在水平 |
1 |
單套裝置生產能力 |
2~3萬噸/年 |
30萬噸/年 |
6~8萬噸/年 |
2 |
單程轉化率(糖醇) |
97% |
≥98.5% |
97.5% |
3 |
選擇性 |
一般 |
強 |
較強 |
4 |
原材料消耗 |
高 |
低 |
較低 |
5 |
能耗T/T |
高 |
低 |
較高 |
6 |
余熱回收率% |
50% |
100% |
70% |
綜述,連續加氫山梨醇生產新工藝是在傳統工藝的基礎上,改造,完善,創新的集成,使山梨醇及其他糖醇的加氫裝置大型化有了保證,生產更安全,實現智能自動化,并大幅降低生產成本,值得推廣應用。
(4)技術聯系:吉林省石油化工設計研究院
聯系電話:王楠 15948315914
李雪 18584360177
(來源:中國石油和化工勘察設計協會) |