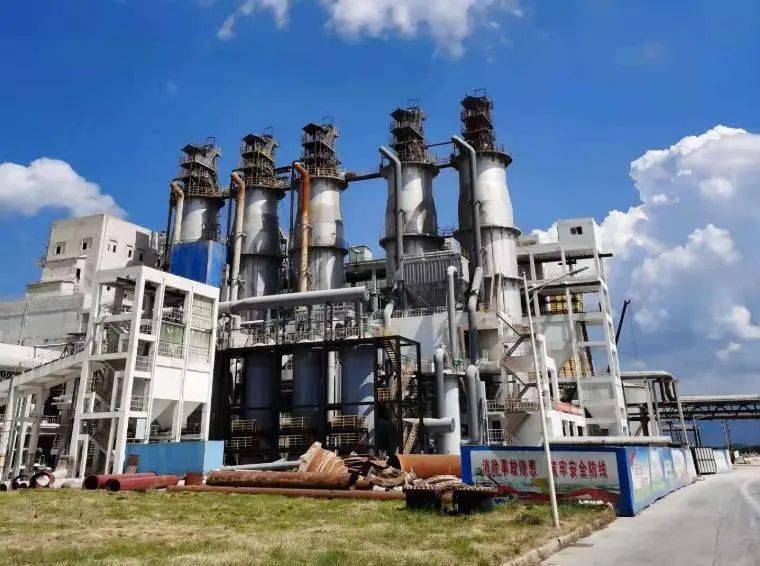
一、技術來源
本技術為液相水合法生產低鹽優質純堿工程新技術,由天津渤化工程有限公司與天津渤化永利化工股份有限公司合作研發,同時集成國內外液相水合法生產低鹽優質純堿行業已經公開的技術進行再創新。
二、基本原理
(1)通過產能的擴大,實現了低鹽優質重灰液相水合法生產工藝的推廣。
(2)解決了水合晶結晶器內部容易結疤,連續運行周期短,需要備用設備輪換清洗,無法實現完全連續生產的問題。
(3)通過增加尾氣處理設備,解決了水合工序水汽、固體顆粒排放無法達到現行國家標準的問題。
(4)通過提高水合結晶器換熱效率,降低了循環水消耗量。
三、工藝過程
自輕灰工序來的輕灰進入優質重灰工序輕灰埋刮板機,從埋刮板輸送機中取出部分輕灰,經螺旋輸送機送入預混設備,完成預混后進入水合結晶器與母液進行水合反應,生成一水堿結晶。結晶器中一水堿晶漿自流入稠厚器,稠厚后自流入離心機進行固液分離,固體一水堿經皮帶機送入冷熱一體流化床干燥脫水。
自流化床出來的重灰由埋刮板輸送機送入震動篩,篩得合格粒度的成品進入皮帶機送入成品包裝倉進行包裝。從離心機濾出的濾液自流到母液桶,由母液泵送至結晶器循環使用。旋風分離器及布袋除塵器回收的堿粉(細粉),由細粉埋刮板機送入包裝工序,根據成品倉檢驗結果,通過均質化處理后進行包裝。
四、技術特點
本專有技術通過在原有重灰生產流程和工序上的創新,實現了生產連續化,降低了原料和輔料的消耗,同時優化了高鹽母液與水合結晶器尾氣的處理,實現了部分碳酸鈉的回收利用。
(1)通過設置前置預混設備,使輕灰與飽和母液實現預混,減少水合結晶器內部的結疤情況,在不影響整個水合反應的前提下,通過對預混器的輪換清洗,實現不設置備用主體設備(水合結晶器)的前提下,確保生產的連續進行,節約了20%設備投資。
(2)通過改變水合結晶器內部上層/下層盤管的布置方法和供水管路、增加夾套內部擾流部件,提高水合結晶器的換熱效率提高15%,減少循環水用量,提高水合反應效果。
(3)將氯化鈉含量高于60g/L的高鹽重灰母液送入蒸發器進行蒸發,分離晶體進行溶解,得到氯化鈉含量低于20g/L的溶液,返回到重灰系統回用。實現了母液除鹽,保障重灰成品低鹽份的同時,回收了母液中的一水碳酸鈉,提高了原料利用率。
(4)使用特殊設計的新型尾氣洗滌塔,在處理尾氣中純堿粉塵的同時,通過對尾氣降溫,實現了對尾氣中水分的回收。
(5)通過采用氣體為載體的輸送方式,擺脫了地形和設備布置的限制,減少了輸送距離,同時保證輸送終端的物料溫度與煅燒爐出口溫度差,保證水合反應的適宜粉體投料溫度,進而縮短水合反應時間。
(6)改進稠厚器的澄清液集液系統,減少了澄清液中一水堿的“逃逸”,降低了成品損耗率。增加了稠厚之后的固液比,降低后續離心分離的處理量。
(7)在重灰成品倉中增加均質混合系統,提高細粉的利用率。
五、技術水平
本工程技術包括多項在液相水合法重質純堿技術首次成功使用的關鍵技術,填補了生產設計上多項技術空白,為我國液相水合法重質純堿技術的不斷發展起到了積極的推動作用。
六、能源消耗
(1)純堿消耗(kg/t):1005
(2)中壓蒸汽3.4MPa(t/t):0.45
(3)綜合能耗:千克標準煤/噸(kg/t):210
七、節能減排狀況
序號 |
工藝技術參數 |
本裝置 |
國內同類裝置 |
備注 |
1 |
循環水消耗量 |
5.4噸/噸產品 |
6噸/噸產品 |
|
2 |
粉塵顆粒排放 |
≤20mg/m³ |
>20mg/m³ |
|
3 |
水回收量 |
2萬噸/年 |
0 |
|
4 |
高鹽母液回用率 |
100% |
0 |
|
八、技術應用條件
適用于國內及國外液相水合法生產低鹽優質純堿工程。
九、應用實例
該技術已成功應用于江蘇實聯化工、天津堿廠搬遷改造、重慶合友等重灰項目。
十、經濟效益
液相水合法生產低鹽優質純堿工程工程設計技術,填補了國內低鹽優質純堿生產設計的空白,為我國純堿工業的技術發展起到了積極的推動作用。
(來源:中國石油和化工勘察設計協會) |